دایکست یکی از روشهای پرکاربرد ریختهگری است که در تولید قطعات دقیق و باکیفیت استفاده میشود. با این حال، نقصهای رایج مانند تخلخل، ترکهای سطحی و ناهماهنگی ابعادی میتوانند باعث کاهش کیفیت محصول و افزایش هزینههای تولید شوند. این مشکلات نهتنها بهرهوری را کاهش میدهند، بلکه در مواردی موجب ازبینرفتن قطعات تولیدشده نیز میشوند. خوشبختانه، با کنترل دقیق فرآیند، بهینهسازی طراحی قالب و استفاده از مواد اولیه باکیفیت، میتوان این نقصها را کاهش داد و تولیدی مقرونبهصرفه و باکیفیت داشت. در این مطلب، مهمترین راهکارها برای بهبود کیفیت قطعات دایکستی را بررسی میکنیم.
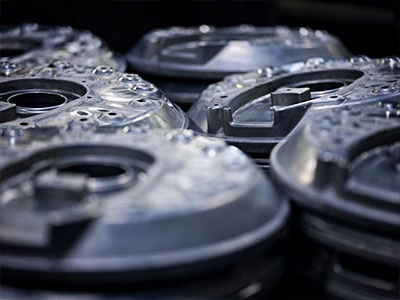
۱. کنترل دما و فشار قالب
یکی از دلایل اصلی نقص در دایکست، تغییرات دما و فشار در قالب است. برای کاهش این مشکلات:
- دمای قالب و فلز مذاب باید در محدوده استاندارد باشد.
- فشار تزریق بهدرستی تنظیم شود تا از ایجاد حفرهها و ترکها جلوگیری شود.
- خنککاری قالب بهطور یکنواخت انجام شود تا از انقباض ناهمگون قطعه جلوگیری کند.
۲. بهینهسازی طراحی قالب
طراحی قالب تأثیر زیادی بر کیفیت قطعه دارد. برخی نکات مهم:
- مسیرهای ورودی مذاب باید بهدرستی طراحی شوند تا از ایجاد تلاطم جلوگیری شود.
- تهویه مناسب برای خروج گازها ضروری است تا از ایجاد حفرههای گازی جلوگیری کند.
- استفاده از پوششهای مخصوص برای بهبود کیفیت سطح قطعه توصیه میشود.
۳. کنترل ترکیب مواد اولیه
کیفیت آلیاژ مورد استفاده در دایکست نقش مهمی در کاهش نقصها دارد:
- ناخالصیهای موجود در فلز باید حداقل باشند.
- ترکیب آلیاژ باید مطابق استانداردهای مشخص باشد تا ویژگیهای مکانیکی مناسب حفظ شوند.
- گازهای محلول در مذاب باید به حداقل برسند تا حبابهای داخلی ایجاد نشوند.
۴. بهینهسازی فرآیند تزریق
فرآیند تزریق فلز مذاب به قالب باید بهدقت تنظیم شود:
- سرعت تزریق باید متناسب با نوع قطعه باشد تا از ایجاد ترک و حفره جلوگیری شود.
- فشار تزریق باید بهگونهای تنظیم شود که تمام جزئیات قالب را پر کند.
- زمان پر شدن قالب نباید بیش از حد طولانی باشد تا از انجماد زودرس مذاب جلوگیری شود.
۵. بهبود سیستم خنککاری و خروج گاز
- خنککاری یکنواخت قالب از تنشهای حرارتی و ترکهای ناشی از انقباض جلوگیری میکند.
- سیستم تهویه مناسب باید طراحی شود تا گازهای محبوسشده در قالب بهراحتی خارج شوند.
۶. استفاده از تجهیزات پیشرفته
- دستگاههای مدرن دایکست با قابلیت کنترل دقیقتر فشار، دما و سرعت تزریق، میتوانند نقصهای تولید را کاهش دهند.
- استفاده از حسگرها برای کنترل همزمان فرآیند میتواند به بهبود کیفیت محصول نهایی کمک کند.
راهکارهای حرفهای با دایکست تات
با کنترل دقیق فرآیند دایکست، از انتخاب مواد اولیه تا تنظیمات دستگاه و طراحی قالب، میتوان میزان نقصها را به حداقل رساند. اجرای این راهکارها باعث افزایش کیفیت قطعات، کاهش هزینههای تولید و بهبود بهرهوری میشود.
رفع نقصهای دایکست نیاز به دانش، تجربه و استفاده از راهکارهای اصولی دارد. اجرای صحیح این روشها باعث بهبود کیفیت، کاهش ضایعات و افزایش بهرهوری در تولید میشود.
در دایکست تات، ما با استفاده از تجهیزات پیشرفته، تیمی متخصص و کنترل دقیق کیفیت، تولید قطعات دایکست را به سطح بالاتری ارتقا دادهایم. اگر به دنبال راهکارهای مؤثر برای بهبود کیفیت قطعات دایکست هستید، ما در دایکست تات آمادهایم تا با خدمات حرفهای خود، نیازهای شما را برآورده کنیم.