اگر به دنبال درک کامل فرآیند تولید قطعات فلزی با دقت بالا هستید، این مطلب به شما نشان میدهد که طرز کار دستگاه دایکاست چگونه است؛ از تزریق فلز مذاب تا خروج قطعه نهایی، همهچیز به زبانی ساده و تخصصی توضیح داده شده است.
تعریف دایکاست
دایکاست به معنای یک فرآیند پردازش فلزی است که در آن فلز مذاب به داخل دستگاه تزریق میشود، اجازه داده میشود تا سرد و سفت شده و سپس به یک مدل خاص تبدیل گردد. قالبهای دایکاست تحت شرایط استاندارد چرخه میشوند تا محصولی آلیاژی از نظر ابعادی یا عملکردی تولید شود.

دایکاست در طیف وسیعی از کاربردها مورد استفاده قرار میگیرد؛ صنایع نورپردازی، خودروسازی، هواپیمایی، تجهیزات سنگین، مبلمان، موتورها، موتور سیکلتها، محصولات با ویژگیهای ویژه و تولید انبوه، باعث شدهاند که دایکاست در زندگی کاربرد گستردهای داشته باشد.
فلز ریختهگری
پرکاربردترین مواد فلزی شامل روی، آلومینیوم، منیزیم، مس، سرب و قلع هستند.
مواد فلزی خاص برای دایکاست شامل:
- آلومینیوم: ADC12، A380، AlSi9Cu3، AlSi12Cu1، AC4CHT6، YL102، YL112، YL113.
- منیزیم: AZ91D، AZ80، AZ31B، AZ40M، AZ31، ZK60، ZK61، AM60M، ME20M، ZK60A، ZK50B، ZK51A.
- روی: Zamak2، Zamak3، Zamak5، Zamak7، Zamak8.
- مس: برنج، برنز.
مزایای دایکاست
- استحکام ضربهای بالاتر نسبت به پلاستیک: بهویژه در ماشینآلات و تجهیزات سنگین مانند کامیونها و خودروها.
- ثبات ابعادی: بسیار مهم است؛ به عنوان مثال، محصولاتی مانند POM یا سایر محصولات پلاستیکی با اشکال ویژه که از آسیا به اروپا منتقل میشوند تحت تأثیر دما تغییر اندازه میدهند، اما قطعات دایکاست تغییر قابل توجهی نخواهند داشت.
- عمر طولانی محصول: قطعات ویژهای مانند بازوهای ربات، پوشش موتور، LED و غیره پس از عملیات طولانی مدت در دماهای بالا و پایین، تغییر در ماده و استحکام نشان نخواهند داد.
- مقاومت بیشتر در برابر خوردگی: برخی از اجزای کشتی، ظروف شیمیایی، قطعات سلاح و غیره که نیاز به غوطهور شدن در مایع یا قرار گرفتن در معرض گاز برای مدت طولانی دارند، بدون اکسیداسیون و تجزیه باقی میمانند.
- عدم تأثیر ضخامت دیوار: برخی قطعات مانند کورههای بزرگ، ساعتها، اجزای هوافضا و کامیونها اغلب به ضخامت و استحکام بسیار بالا نیاز دارند که تنها با دایکاست قابل دستیابی است.
معایب دایکاست
- خطرات در محیط کارگاه: فرآیند ریختهگری دایکاست در کارگاه خطرناکتر بوده و الزامات ایمنی، بیمه و حفاظت بیشتری را میطلبد.
- وزن بیشتر نسبت به محصولات پلاستیکی: این امر منجر به افزایش هزینههای حمل و نقل و بستهبندی میشود.
- تقاضای بالاتر از نظر محیطی: کارگاههای دایکاست ممکن است کثیفتر و آشفتهتر باشند و تخلیه اگزوز و پساب به آسانی انجام نشود.
- عدم امکان استفاده از ساختارهای قالب پیچیده: برای همان محصول، قالبهای پلاستیکی میتوانند پیچیدگی ساختاری بیشتری ارائه دهند، در حالی که قالبهای دایکاست نیازمند ماشینکاری ثانویه مانند CNC و WEDM هستند.
- هزینههای بالاتر نسبت به پلاستیک: شامل هزینههای مواد، ابزار، حمل و نقل، محیط زیست و پردازشهای پس از تولید.
انواع ریختهگری
- ریختهگری دایکاست:
یک فرآیند ریختهگری با دقت بالا که معمولاً برای تولید قطعات دایکاست با الزامات ابعادی مانند هوافضا، خودروسازی، تجهیزات سفارشی و سایر قطعات دقیق استفاده میشود. آشنایی با طرز کار دستگاه دایکاست برای شما روشن خواهد کرد که در این فرآیند، تمامی مراحل از جمله تزریق، نگهداشتن فشار و خنککننده در دستگاه انجام میشود. - ریختهگری شن و ماسه:
روشی کمهزینه که به صورت نیمهدستی و نیمهماشینی انجام میشود. در این روش، چندین چیدمان مختلف در یک حفره قالب وجود دارد و تولید قالبها و هستهها بدون هزینههای بالا انجام میشود. همچنین نیازی به ظاهر یا سختی بالا برای قالب نیست؛ پس از شکلگیری، ممکن است نیاز به پرداخت ظاهری داشته باشد و تقریباً محدودیتی در چگالی و دقت محصول وجود ندارد. این روش برای طیف گستردهای از مواد ریختهگری قابل استفاده است. - ریختهگری مومی:
یک فرآیند پیچیده برای تولید قطعات دایکاست با اشکال و ساختارهای پیچیده. در مرحله اول، یک قالب مومی با ساختاری مشابه قالب پلاستیکی ساخته میشود، با موم پر شده و شکل داده میشود (شکل موم همان شکل نهایی دایکاست است). در مرحله دوم، محصول از قالب خارج شده و بهطور یکنواخت با دو ماده ویژه پوشش داده میشود؛ پوشش اول به صاف شدن سطح دایکاست کمک میکند و از ترک خوردن محصول جلوگیری میکند، و پوشش دوم قالب پوسته قطعه را شکل میدهد که نقطه ذوب آن کمی بالاتر از دایکاست است. در مرحله سوم، محصول به کوره فرستاده میشود تا مواد سطحی در دمای بالا پوسته را تشکیل دهند و موم ذوب شود. در نهایت، ریختهگری مومی بهوجود میآید؛ فلز مذاب ریخته شده و برای عایق کردن پوشش داده میشود و سپس پوسته شکسته شده و قطعه جدا میگردد. - ریختهگری با فشار پایین:
روشی ساده که از دایکاست با فشار بالا در سه جنبه متفاوت است:- فلز مذاب با استفاده از هوا به قالب تزریق میشود.
- کوره در پایین قالب قرار میگیرد تا فشار هوا تسهیل شود.
- شکل محصول باید به صورت آینهای ظاهر شود تا تعادل فشار در داخل قالب فراهم گردد.
این روش برای اکثر قطعات دایکاست مناسب نیست؛ دلیل آن نیز در همینجا بیان شده است.
- ریختهگری گرانشی:
سادهترین نوع ریختهگری است که تنها شامل یک حفره و یک هسته میشود و نیازی به دستگاه برای ثابت کردن آن نیست. در این روش، فلز مذاب از بالای قالب ریخته شده و پس از سرد شدن از آن خارج میشود. این روش برای تولید دستههای کوچک قطعات دایکاست مناسب است. - ریختهگری تحت خلاء:
روشی برای بهبود کیفیت قطعات ریختهگری، معمولاً برای آلیاژهای منیزیم. در این روش، قبل از تزریق فلز مذاب، هوا از داخل حفره قالب خارج میشود (برخی قالبهای ویژه پس از تخلیه هوا با اکسیژن تزریق میشوند) و سپس فلز وارد قالب میگردد؛ نتیجه آن، قطعه دایکاستی با تخلخل کمتر و چگالی بالا است. این روش در تولید دستهای پیچیدهتر بوده و به دلیل نشت هوا مستعد انفجار میباشد.
تفاوت بین انواع ریختهگری
- ریختهگری تحت خلاء: از نظر کیفیت بهترین است.
- دایکاست: بالاترین کارایی را دارد و برای ریختهگری قطعات با ریتین باریک مناسب است.
- ریختهگری گرانشی: از نظر هزینه به صرفهترین است.
- ریختهگری شن و ماسه: برای تولید دستههای کوچک مناسب است.
- ریختهگری مومی: بهترین انتخاب برای ساختارهای پیچیده میباشد.
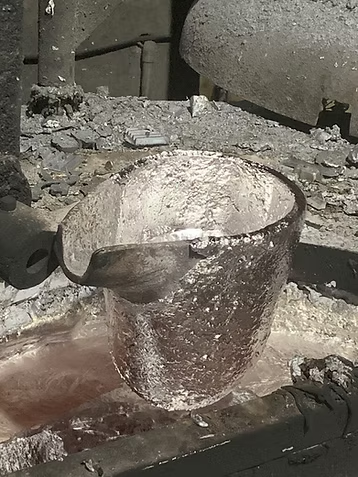
عوامل مؤثر بر کیفیت طرز کار دستگاه دایکاست:
- دستگاه پایدار و تأمین مواد اولیه بهصورت مداوم، بدون وجود تخلخل و باقیمانده.
- هسته و حفره قالب در طول فرآیند حرارتی در دمای مشخص قرار دارند تا ماده در بهترین شرایط عملکردی باشد. انتخاب استیل مناسب دایکاست برای هسته و حفره اهمیت ویژهای دارد، زیرا تولید همواره در محیطی با دمای بالا صورت میگیرد.
- در صورتی که ماده فلزی بدون ناخالصی بوده و دما مناسب باشد، سطح دایکاست صافتر خواهد بود.
- طراحی مناسب دروازه، تسمه سرباره و اجکتور در قالب، موجب یک فرایند ریختهگری یکنواخت بدون فشار بیش از حد و ضایعات مواد میشود.
نکات طراحی قالب دایکاست
در فرآیند طراحی قالبهای سهبعدی باید از موارد زیر اجتناب کرد:
- گوشههای تیز.
- کم بودن یا نبودن زاویه پیشنشینی: منظور از “زاویه پیشنشینی” در طراحی قالب، شیب کوچکی است که برای تسهیل خارج شدن قطعه از قالب اعمال میشود. عدم وجود این زاویه میتواند منجر به مشکلاتی در جداسازی و تولید قطعات با کیفیت پایین شود.
- دیوارهای سنگین.
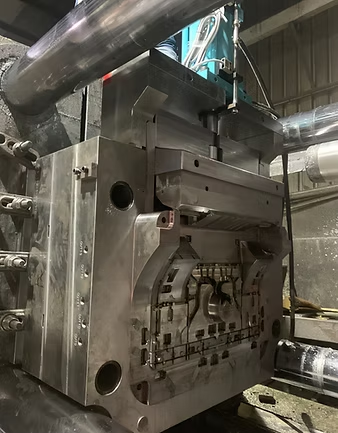
موارد زیر در طراحی قالب باید مد نظر قرار گیرند (تهیه گزارش تحلیل Moldflow):
- دروازه (Gate).
- مسیر جریان (Runner).
- محل اگزوز (Exhaust seat).
- سیستم خنککننده.
موارد زیر نیز پیش از آزمایش باید طراحی شوند:
- استفاده از ستونهای حمایتی به حداکثر میزان ممکن.
- تنظیم دمای پیشگرمایش بر اساس نیازهای ماده.
- کنترل زمان چرخه.
- کنترل دمای قالب و فلز.
- تعیین اندازه ماشین.
تفاوت دایکاست و محصولات پلاستیکی از منظر محیط زیست
به گفته دانشمندان، ماهیها، پرندگان و حیوانات به دلیل مصرف تصادفی پلاستیکهای شناور در اقیانوس جان خود را از دست دادهاند. قطعات دایکاست به ندرت در اقیانوس رها میشوند و حتی اگر رها گردند، به ته دریا فرو میروند و دوباره بازیافت میشوند؛ بنابراین، دفع دایکاست تأثیر زیستمحیطی بسیار کمی خواهد داشت، در حالی که دفع پلاستیک تأثیر بسیار منفی بر محیط زیست دارد.
چرا رنگ قطعات دایکاست تغییر میکند؟
هنگامی که ماده دایکاست ذوب میشود، مقداری پرز آهن با آن مخلوط شده و وارد کوره میشود. پس از تکمیل ریختهگری، آهن با اکسیژن موجود در هوا اکسید شده و رنگ سطح دایکاست تغییر میکند. در صورت نیاز به الزامات سختگیرانهتر، ریختهگری تحت خلاء توصیه میشود.
فرآیندهای پس از تولید دایکاست
- پانچ اولیه و دقیق.
- پرداخت لبهها (Deburring) و تمیزکاری سوراخها.
- ماشینکاری با CNC، EDM و WEDM.
- حفاظت سطحی در برابر خوردگی.
- سندبلاست، اویل بلاست، الکتروپلتینگ و حتی اکسیداسیون مثبت.
طرز کار دستگاه دایکاست در عمل
آشنایی با طرز کار دستگاه دایکاست کلید درک فرآیندهای پیشرفته تولید قطعات فلزی با دقت بالاست. این فناوری، از تزریق فلز مذاب تا خروج محصول نهایی، امکان تولید اجزایی با ثبات ابعادی، استحکام بالا و عمر طولانی را فراهم میآورد. شرکت دایکست تات با بهرهگیری از تجهیزات مدرن و تیمی متخصص، خدمات جامعی از طراحی قالب تا کنترل دقیق کیفیت ارائه میدهد. این مجموعه، با رویکردی یکپارچه در زمینه دایکاست، تضمین میکند که محصولات نهایی شما با استانداردهای جهانی و بهصرفه تولید شوند. اگر به دنبال ارتقای بهرهوری و کاهش هزینههای تولید هستید، دایکست تات همراه مطمئن شما در مسیر تولید قطعات فلزی دقیق و بادوام خواهد بود.